In the high-stakes world of aviation, every minute of aircraft downtime translates directly to lost revenue and operational disruption.
For fleet operators and maintenance managers, the key to maximizing aircraft availability lies not just in reactive maintenance but in building a comprehensive strategy around reliable replacement parts and intelligent inventory management.
The True Cost of Aircraft Downtime
Every hour an aircraft spends on the ground costs commercial operators roughly $10,000-$15,000 in lost revenue, but the financial impact extends far beyond just canceled flights. Most operators face immediate hits from continuing crew payments, airport parking fees, and emergency parts logistics – expenses that quickly compound when dealing with unplanned maintenance.
What’s often overlooked are the hidden costs that can actually hurt more in the long run. Stranded passengers don’t just mean immediate compensation costs; they create lasting reputation damage through negative reviews and social media complaints. In today’s competitive aviation market, even a single high-profile service disruption can jeopardize valuable corporate contracts and customer loyalty.
The maintenance ripple effects can be equally devastating. One aircraft’s extended downtime often forces operators to adjust the maintenance schedules of their entire fleet. This domino effect can disrupt carefully planned maintenance intervals for weeks or even months. Take the recent case of a regional carrier whose two-day parts delay for a single aircraft led to a maintenance backlog that took six weeks to fully resolve, costing them over $300,000 in additional operating expenses.
For private operators and smaller airlines, these impacts can be even more severe. A charter operator recently lost a major client after a critical part delay caused them to miss an important business meeting—proving in aviation, downtime costs aren’t just measured in dollars but in lost opportunities and damaged relationships.
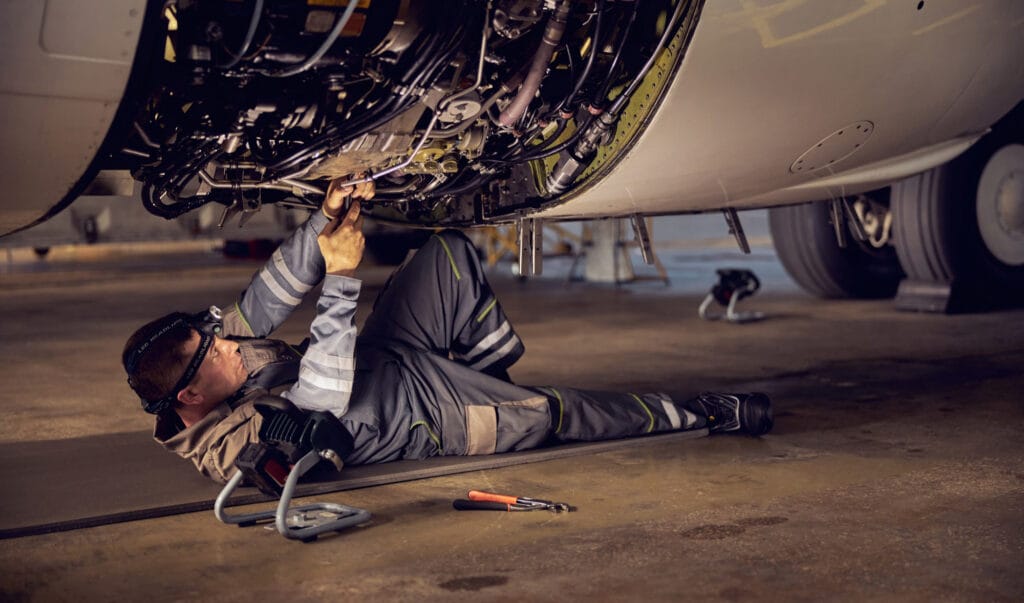
Key Factors in Replacement Parts Selection
Selecting the right aircraft parts involves more than just finding compatible components. When aircraft reliability and safety are at stake, operators need to consider several critical factors that impact immediate operations and long-term maintenance success.
OEM vs. PMA: Making the Right Choice
The choice between OEM (Original Equipment Manufacturer) and PMA (Parts Manufacturer Approval) parts is crucial for maintenance efficiency. While OEM parts come straight from manufacturers like Boeing or Airbus, offering guaranteed compatibility and full warranty coverage, PMA alternatives certified by the FAA can save 30-40% without compromising on quality. Smart operators often mix both, using OEM for critical systems while leveraging PMA parts for routine replacements.
Certification: Non-Negotiable Requirements
Every replacement part needs proper documentation. An FAA Form 8130-3 or EASA Form 1 is essential for verifying airworthiness. Top suppliers maintain detailed records of manufacturing dates, batch numbers, and testing results. This paperwork isn’t just red tape; it’s your insurance policy for maintaining compliance and aircraft safety.
Traceability Matters
Component traceability impacts both safety and maintenance planning. Each part should have a documented journey from the manufacturer to your aircraft. This history becomes invaluable when tracking potential issues or responding to service bulletins. Digital tracking systems now make this process easier, helping maintenance teams quickly identify and address concerns across their fleet.
The Real Cost Equation
Don’t let a lower price tag fool you. The true cost of a replacement part goes beyond its purchase price. Factor in reliability data, mean time between failures, and potential maintenance impact. A cheaper part that needs frequent replacement or causes additional maintenance can quickly become the more expensive choice.
Choosing the Right Supplier
Your parts supplier should be more than just a vendor. They’re a critical partner in maintaining your aircraft’s reliability. Look for suppliers with proven expertise in your aircraft type, strong industry references, and robust AOG (Aircraft on Ground) support. The best suppliers combine competitive pricing with technical support and flexible shipping options, helping you minimize costly downtime when it matters most.
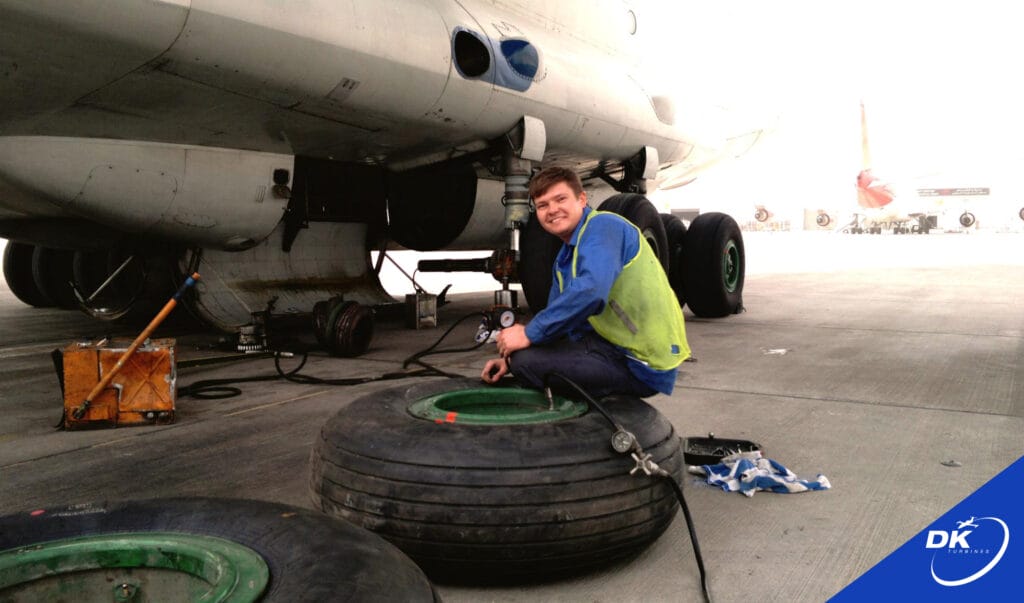
Strategic Parts Management Practices
In today’s fast-paced aviation environment, reactive parts management isn’t just inefficient – it’s a liability. Successful operators are adopting sophisticated strategies that balance cost control with operational readiness, ensuring they have the right parts at the right time.
Optimizing Your Parts Inventory
Smart inventory management means walking the line between overstocking and running too lean. Leading operators maintain detailed usage data to identify optimal stock levels for routine components.
They factor in lead times, seasonal maintenance patterns, and historical consumption rates. Spare parts for corporate aircraft operators require a strategic approach to ensure availability without tying up excess capital. The goal isn’t to stock everything – it’s to stock intelligently based on actual needs and critical priorities.
Embracing Predictive Maintenance
Gone are the days of waiting for parts to fail. Modern predictive maintenance uses real-time data and trend analysis to anticipate component needs before they become urgent.
By monitoring part performance, wear patterns, and maintenance intervals, operators can schedule replacements during planned downtime rather than scrambling during emergencies. This approach not only reduces unexpected failures but also extends component life through timely intervention.
Developing Your Critical Parts List
Not all parts deserve equal attention in your inventory strategy. A well-crafted critical parts list identifies components that could ground your aircraft or significantly impact safety.
Consider factors like lead time, cost, failure impact, and historical reliability. This list becomes your roadmap for inventory decisions, helping prioritize stock levels and supplier relationships for truly essential components.
Planning for AOG Situations
Even with the best planning, AOG situations happen. Smart operators maintain detailed contingency plans that include:
- Pre-arranged agreements with key suppliers for emergency shipments
- Relationships with reliable parts brokers worldwide
- Clear procedures for expedited customs clearance
- Backup transportation options for critical components
Leveraging Digital Management Systems
Modern inventory management requires modern tools. Digital systems provide real-time visibility into stock levels, automate reordering processes, and track part lifecycles. The best platforms integrate with maintenance planning software, creating a seamless flow between parts forecasting and maintenance execution. These systems also maintain detailed audit trails, simplifying compliance reporting and quality control.
Quality Assurance Best Practices
Quality assurance in aircraft parts management requires uncompromising attention to detail and consistent execution. Every component that enters your facility must be treated as critical to flight safety, backed by thorough documentation and proper handling throughout its lifecycle.
- Implement a rigorous receiving inspection process where qualified inspectors verify physical conditions, part numbers, and manufacturing details against purchase orders. Document every inspection with photos and detailed notes – even minor discrepancies could indicate serious issues.
- Always verify complete certification documentation, including 8130-3 or EASA Form 1 forms, material certifications, and conformity declarations. Create a standardized checklist for documentation review to ensure nothing gets missed during the verification process.
- Maintain strict storage and handling protocols, including climate-controlled environments for sensitive components and ESD protection where needed. Monitor shelf life meticulously and implement a first-in-first-out (FIFO) system for inventory management.
- Establish comprehensive staff training programs that include initial certification, regular refresher courses, and documented competency assessments. Keep your team updated on the latest manufacturer bulletins and regulatory changes through structured continuing education.
- Use digital quality management systems to track parts from receiving through installation. These systems should maintain detailed audit trails, automate inspection scheduling, and integrate seamlessly with your maintenance planning software.
- Conduct regular internal audits of your quality processes to identify potential improvements and ensure compliance with industry standards. Document all findings and create action plans to address any gaps in your quality system.
- Create clear procedures for handling non-conforming parts, including quarantine processes, supplier communication protocols, and corrective action tracking. Every quality issue should be treated as an opportunity to strengthen your system.
Maximizing Air Time: Your Path to Operational Excellence
Minimizing aircraft downtime isn’t just about having the right parts – it’s about building a comprehensive system that keeps your fleet in the air where it belongs. By carefully selecting quality components, implementing strategic inventory management, and maintaining rigorous quality standards, you can significantly reduce the operational and financial impact of unplanned maintenance.
The path to optimal fleet reliability starts with a single step: committing to excellence in your parts management strategy and backing that commitment with consistent, quality-focused execution. Start today with DK Turbines!