Aircraft components are built for precision and durability, but improper storage can lead to premature wear, corrosion, and costly failures. Factors like humidity, temperature fluctuations, and contamination can quietly degrade essential parts, even when they’re not in use—minimizing the need for costly aircraft part repairs.
By understanding environmental risks and following best practices, aviation professionals can keep their inventory in top condition, making sure every component is ready to perform when it matters most.
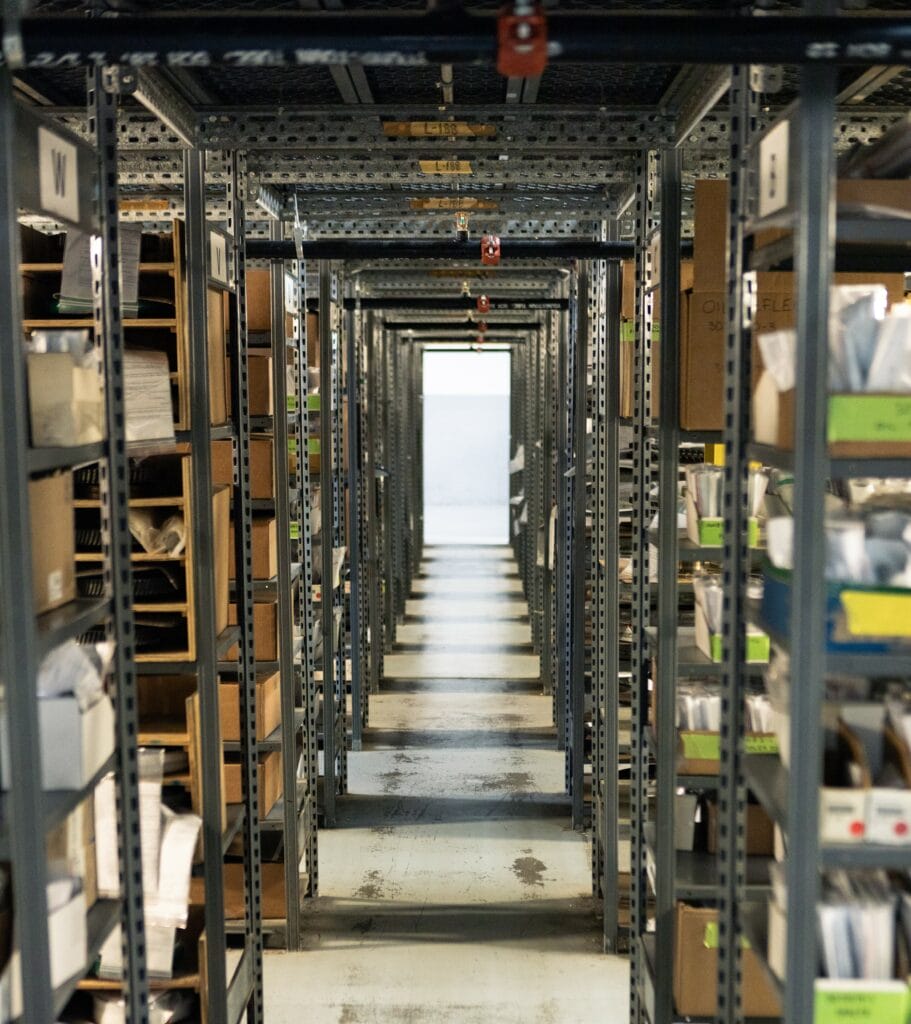
Environmental Threats to Aircraft Parts
Knowing the potential environmental threats is essential for implementing effective preservation strategies.
Moisture and Corrosion Dangers
Moisture in the air creates the perfect environment for corrosion on metal surfaces. Even minimal exposure can trigger oxidation processes on critical engine components and structural elements.
At humidity levels above 60%, the corrosion rate accelerates dramatically, potentially rendering expensive parts unusable. Salt-laden air near coastal areas poses additional challenges, as sodium chloride compounds accelerate the degradation of aluminum alloys common in aviation.
Temperature Damage Risks
Rapid or extreme temperature fluctuations create expansion and contraction cycles that stress component materials. These thermal cycles can compromise the structural integrity of composite materials, weaken adhesive bonds, and affect calibration in precision instruments.
Most aircraft parts perform optimally when stored between 50-70°F (10-21°C), with minimal fluctuation. Extreme heat accelerates rubber and seal deterioration while freezing temperatures can cause brittleness in polymers and elastomers.
Contamination Hazards
Dust, dirt, and airborne contaminants can infiltrate sensitive components, causing abrasive damage to moving parts and precision surfaces. Even microscopic particles can interfere with electrical connections and block critical fluid passages in hydraulic and fuel systems. Oil and chemical residues attract additional contaminants, creating a cascade effect that compounds damage over time.
UV Radiation Effects
Prolonged exposure to sunlight causes photodegradation in polymers, composites, and painted surfaces. UV radiation breaks down molecular bonds in materials, leading to embrittlement, color fading, and reduced tensile strength. Windscreens, cabin interiors, and exterior coating systems are particularly vulnerable. Even artificial lighting can contribute to cumulative damage over extended storage periods.
Categorizing Aircraft Parts by Storage Requirements
Aircraft components vary dramatically in their storage needs based on materials, precision requirements, and environmental sensitivities. Understanding these differences helps maintenance teams develop specialized storage protocols for maximum part longevity.
Engine Component Protection
Engine parts demand careful storage due to their precision and critical function. Turbine blades need humidity below 40% to prevent corrosion. Additionally, combustion chambers require preservative oils and vapor-barrier packaging. Bearings need monthly rotation to prevent flat spots. Electronic controls must have anti-static packaging and stable temperatures between 60-75°F.
Avionics and Electrical Safeguarding
These sensitive systems need static-controlled environments with low humidity. Circuit boards require anti-static bags with desiccants. Connectors need protective caps to prevent damage. Moreover, screens should be stored face-down on soft surfaces. Since avionics contain calibration that can drift with vibration or temperature changes, they require isolated storage racks.
Structural Component Storage
Airframe components need proper support to prevent warping during storage. Aluminum parts require neutral pH wrapping to prevent galvanic corrosion. Composites must be kept away from degrading solvents. Because dimensional stability is critical, load-bearing components need adequate support. Landing gear requires specialized cradles and regular lubrication.
Polymer and Rubber Preservation
Elastomeric parts degrade quickly without proper care. O-rings and seals should be stored away from ozone and UV light sources. Hydraulic hoses need end caps and loose coiling to prevent stress damage. Maintaining temperature control between 50-70°F significantly extends shelf life. Finally, tires should be rotated quarterly and stored vertically in dark environments to prevent flat spots.
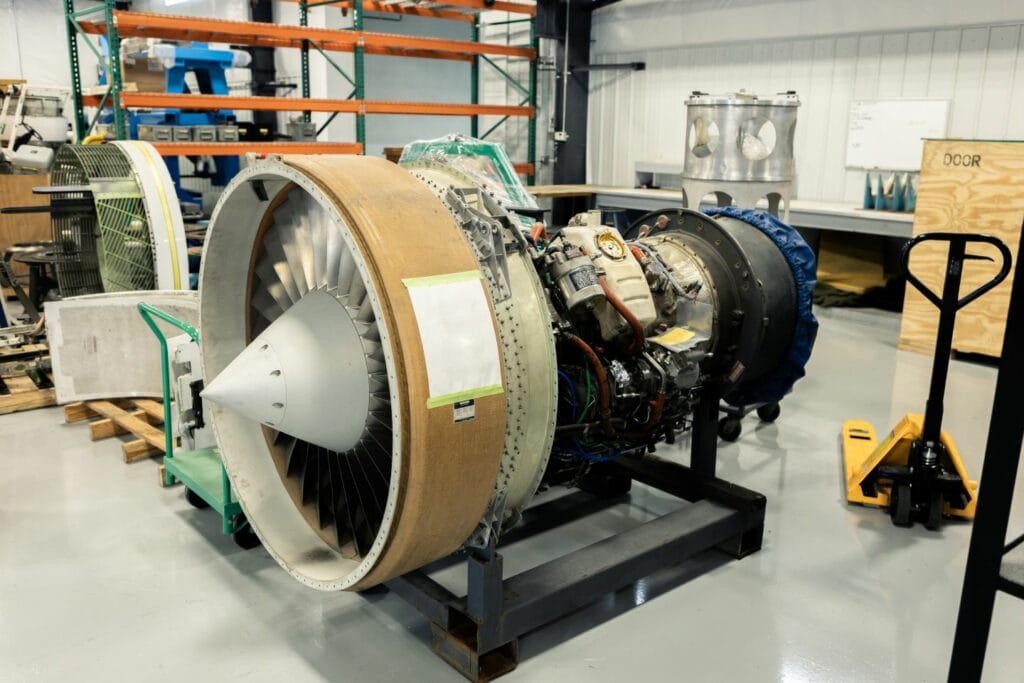
Common Storage Mistakes and How to Avoid Them
Even with the best intentions, improper storage of aircraft parts happens more often than you’d think. A small mistake—like overlooking humidity levels or skipping a simple rotation schedule—can turn a perfectly good component into an expensive, unusable piece of scrap.
Failing to Control Humidity
One of the biggest mistakes is failing to control humidity. Moisture is the silent destroyer of metal components, especially in coastal or high-humidity environments. Without proper control, corrosion can set in fast—even on parts that aren’t directly exposed to the elements. The best way to prevent this is by maintaining stable humidity between 35-45% using dehumidifiers and vapor-barrier packaging for metal components. Humidity sensors are also invaluable for catching fluctuations before they cause damage.
Skipping Rotation and Inspection Schedules
Skipping rotation and inspection schedules is another common issue. Bearings, gears, and tires can develop flat spots if they sit in one position for too long. Seals and rubber components dry out over time, becoming brittle and prone to leaks. Sticking to a regular rotation schedule—moving parts every few months—prevents stress damage. Routine inspections also catch early signs of corrosion, warping, or material degradation before they become major problems.
Ignoring Static Protection for Avionics
Avionics storage mistakes often involve static damage. Electronic components are highly sensitive to electrostatic discharge, and one misplaced part on a metal shelf or an ungrounded technician handling a circuit board can cause invisible, irreversible damage. In fact, improper storage is a frequent room cause when troubleshooting common avionic problems. To prevent this, avionics should always be stored in anti-static bags with desiccant packets. ESD-safe shelving, climate-controlled environments, and proper handling procedures—like wearing anti-static gloves—further reduce the risk of damage.
Improper Support for Structural Components
Structural components, especially large aluminum and composite sections, require proper support. Without it, parts can warp, leading to hidden structural weaknesses. Large components should be placed on custom cradles that distribute weight evenly. Aluminum parts should be wrapped in neutral pH materials to prevent galvanic corrosion, while composite materials need careful positioning to maintain their shape.
Exposing Rubber and Polymer Parts to Light and Ozone
Rubber and polymer parts also need special care. O-rings, seals, and hoses degrade when exposed to UV light, ozone, or temperature extremes. Storing them near electric motors or fluorescent lighting speeds up this process. Keeping these parts in sealed containers in dark, temperature-controlled environments between 50-70°F extends their lifespan. Rotating them regularly helps identify brittleness before they fail in operation.
Best Storage Practices
Storing aircraft parts the right way isn’t just about organization—it’s about keeping them in peak condition and avoiding costly replacements.
A climate-controlled environment, maintained with HVAC systems and continuous monitoring, keeps humidity between 35-45% and temperatures steady at 65-75°F.
In coastal areas, dehumidifiers help combat the salt in the air that speeds up corrosion.
Proper packaging goes a long way in protecting parts. Moisture-sensitive components should be sealed in vapor-barrier bags, while avionics need anti-static packaging to prevent damage. Metal surfaces benefit from corrosion inhibitors, and whenever possible, storing parts in their original packaging helps maintain factory-fresh quality.
Rotation and regular inspections prevent unnecessary wear. Bearings, gears, and tires need to be rotated every few months to prevent flat spots, and monthly visual checks help catch early signs of corrosion or damage. Preservatives should be reapplied as recommended, and using the FIFO (First In, First Out) method keeps older stock from sitting too long.
Good documentation keeps everything running smoothly. Tracking storage conditions, expiration dates, and maintenance history ensures nothing gets overlooked. Digital records, including storage requirements for each component, make it easier to stay organized and compliant with industry standards.
With the right storage practices in place, aircraft components stay in top shape, avoiding premature failure and keeping operations efficient.
Preserving Aircraft Parts for the Long Haul
Proper storage isn’t just a routine task—it’s a critical investment in the longevity, safety, and performance of aircraft components. By controlling environmental factors, using the right packaging, and following structured maintenance schedules, aviation professionals can prevent costly failures and keep parts in peak condition. Small mistakes in storage can lead to big problems down the line, but with the right approach, those risks are easily avoided. In the end, a well-maintained inventory ensures that every component is ready for action when it’s needed most.