Turbine engines don’t just power aircraft—they go through a complex lifecycle that begins long before takeoff. From the initial design phase to rigorous testing, production, and decades of operation, each stage plays a crucial role in ensuring reliability and efficiency.
This journey explores the lifecycle of a turbine engine, detailing how turbine engines are built, maintained, and eventually retired, shaping the future of aviation with every flight.
1. Design: Where Innovation Takes Flight
Every turbine engine begins as an idea—an ambitious vision to push the boundaries of aviation performance, efficiency, and reliability. The design phase is where engineers and manufacturers collaborate to bring this vision to life, balancing aerodynamics, fuel efficiency, and power output while considering the demands of modern air travel.
This process starts with extensive research into airflow dynamics, thermal resistance, and material science. Engineers rely on computational fluid dynamics (CFD) simulations to model how air moves through the engine, identifying ways to optimize thrust and minimize fuel consumption. Every contour of the compressor blades, every angle of the turbine vanes, and every chamber of the combustion system is carefully refined to maximize efficiency.
Beyond performance, the design phase must also account for durability. Turbine engines endure extreme heat, pressure, and stress during flight, making material selection a critical factor. Aerospace-grade alloys, ceramic coatings, and composite materials are chosen not just for strength but for their ability to withstand years of high-speed rotations and temperature fluctuations.
As technology advances, sustainability has become a core focus in turbine engine design. Manufacturers explore alternative fuels, hybrid propulsion systems, and lighter materials to reduce emissions and fuel consumption.
The engines designed today are not just about power—they are about shaping the future of aviation with a greater emphasis on environmental responsibility.
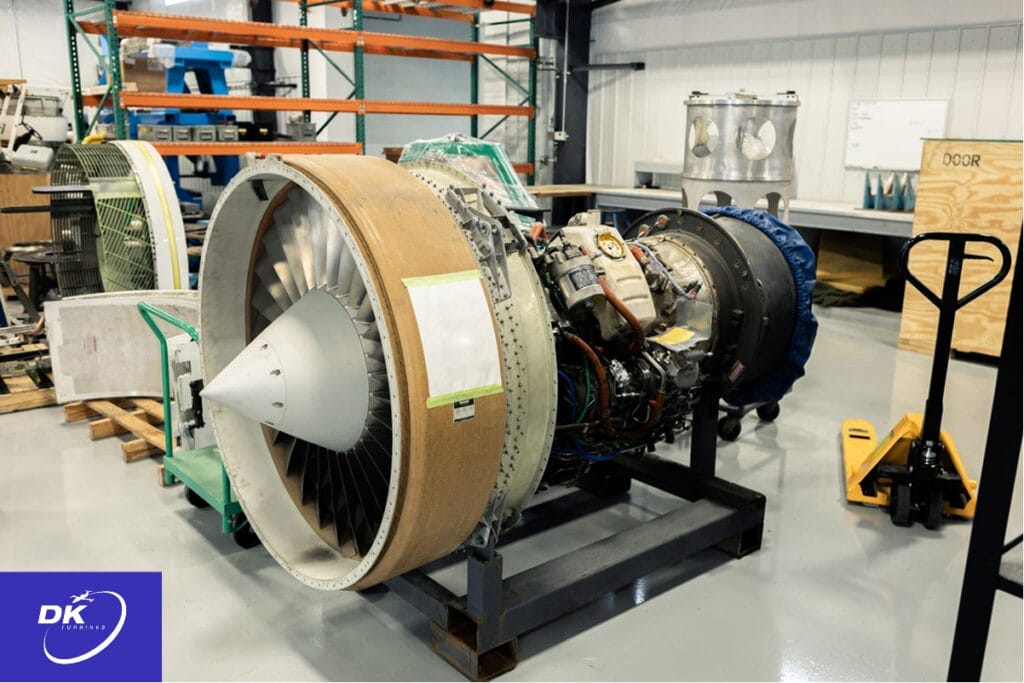
2. Prototype: Turning Blueprints into Reality
Once the turbine engine’s design is finalized, the next step is bringing it to life through a prototype. This phase is where theoretical models meet real-world applications, allowing engineers to test how their ideas perform under actual conditions.
Building a prototype is no small feat. Each component, from the fan blades to the combustion chamber, is precision-manufactured using state-of-the-art machining and additive manufacturing techniques. The materials selected in the design phase—whether advanced nickel alloys, ceramic composites, or lightweight titanium—are now shaped into physical parts assembled with meticulous accuracy.
At this stage, engineers conduct initial system integrations to confirm that all components work together as expected. The engine is mounted on test stands, where it undergoes controlled operational assessments, from startup sequences to airflow evaluations. Sensors are placed throughout the engine to collect data on temperature fluctuations, vibration levels, and pressure changes, providing insight into performance and potential areas for refinement.
Prototyping is also the point where design modifications happen. If unexpected inefficiencies arise—such as excessive heat in certain areas or airflow disruptions—engineers make necessary adjustments. This iterative process allows for fine-tuning before full-scale testing begins. It’s also during this phase that the practical differences between turbine engines become more pronounced, as design variations can significantly impact thermal behavior, airflow efficiency, and material stress responses.
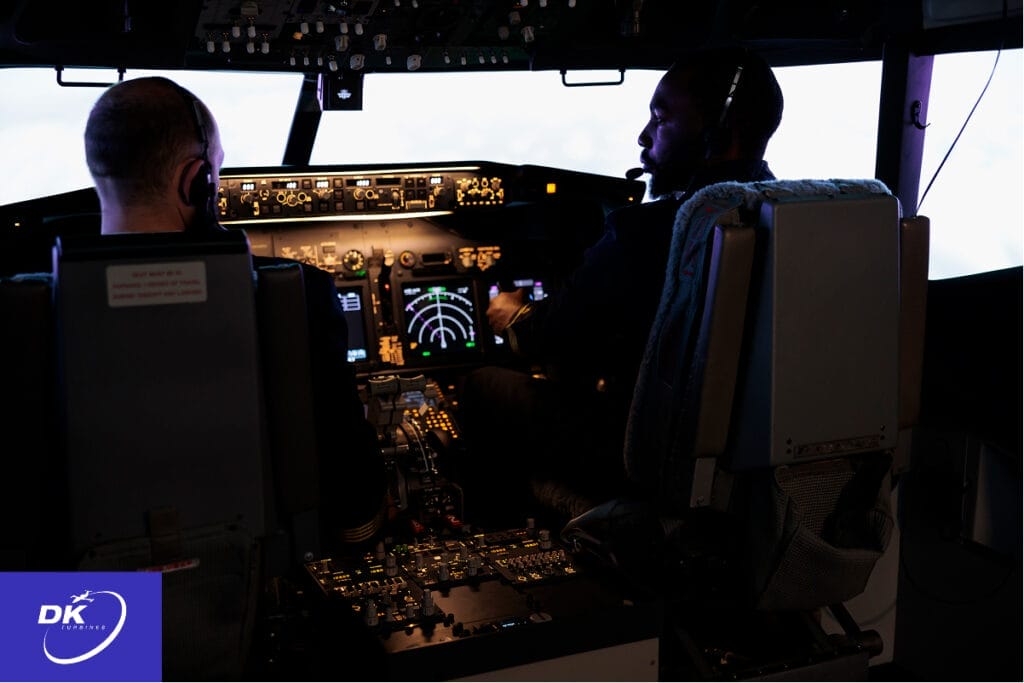
3. Testing: Pushing the Limits of Performance
With the prototype built, it’s time for one of the most demanding phases in a turbine engine’s lifecycle—testing. This is where engineers push the engine to its limits, exposing it to extreme conditions to confirm that it can perform safely and reliably in real-world aviation.
Testing begins in a controlled environment, where the engine is mounted on a specialized test stand. During these early assessments, engineers evaluate fundamental functions like ignition sequences, fuel efficiency, and airflow stability. High-speed cameras, thermal sensors, and vibration detectors collect real-time data, allowing teams to analyze how the engine responds under different operating conditions.
One of the most critical aspects of testing is stress endurance. The engine undergoes simulated flight scenarios that replicate everything from high-altitude cruising to rapid acceleration and deceleration. It is subjected to extreme temperatures, powerful air pressures, and sudden shifts in load to measure its resilience. Engineers also conduct blade-off tests, in which a fan blade is intentionally detached at full speed to assess the engine’s ability to contain the failure without endangering the aircraft.
In addition to durability, fuel efficiency, and emissions testing play a significant role. With the push toward sustainable aviation, engines must meet increasingly strict environmental regulations. Testing helps optimize combustion efficiency, reduce carbon emissions, and enhance overall fuel economy.
Only after passing these rigorous trials does a turbine engine move on to the next stage: certification. At this point, every piece of data is reviewed to confirm that the engine meets aviation standards, bringing it one step closer to real-world deployment.
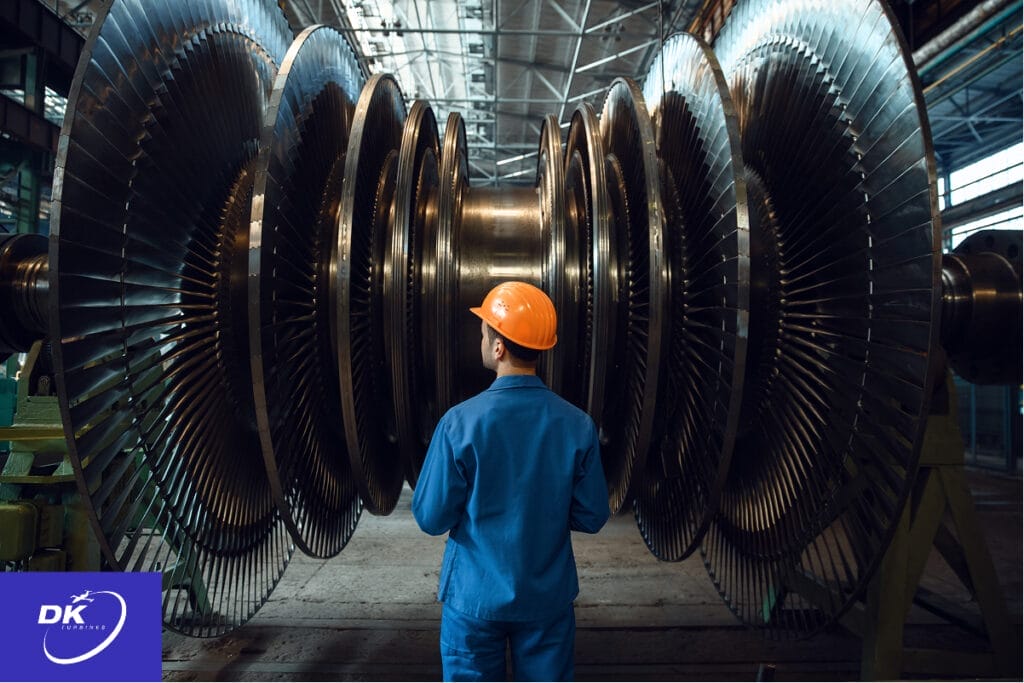
4. Certification: Meeting the Highest Standards
After surviving the grueling testing phase, the turbine engine enters certification—a critical step where regulatory agencies determine if it meets the strict safety, performance, and environmental standards required for aviation. Without certification, an engine cannot be installed on an aircraft, making this one of the most scrutinized stages in its lifecycle.
Government agencies such as the Federal Aviation Administration (FAA) in the United States and the European Union Aviation Safety Agency (EASA) in Europe oversee this process. Their engineers and inspectors conduct exhaustive reviews of test data, material specifications, and structural integrity reports to confirm that the engine can operate under real-world conditions without failure.
Beyond reviewing past tests, aircraft certification agencies require additional trials to validate long-term reliability. These trials include extended endurance runs, simulated flight cycles, and environmental stress tests that expose the engine to high altitudes, extreme temperatures, and variable humidity levels.
Emissions compliance is another major factor in certification. With the aviation industry striving to reduce its carbon footprint, turbine engines must pass stringent fuel efficiency and emissions regulations. Noise levels are also carefully analyzed, as modern aircraft engines must meet community noise reduction standards to minimize their impact on residential areas near airports.
5. Production: Precision at Scale
With certification complete, turbine engines move into full-scale production, where precision manufacturing transforms prototypes into fully operational powerplants. This phase demands a balance of automation and human expertise to maintain the highest quality standards while producing engines at scale.
Advanced alloys, ceramic composites, and high-temperature coatings are machined, forged, and cast with extreme accuracy. Automated systems handle much of the cutting and assembly, but aerospace engineers oversee every detail to confirm structural integrity. Each component, from fan blades to combustion chambers, undergoes rigorous quality control, including X-ray imaging and ultrasonic testing to detect even microscopic flaws.
Once assembled, engines undergo a final round of performance testing before delivery to aircraft manufacturers. With production complete, the engines are integrated into the aircraft, marking the start of their operational life.
6. Maintenance: Keeping Power in the Air
Once a turbine engine enters service, maintenance becomes a crucial part of its lifecycle. Unlike other mechanical systems, aircraft engines operate under extreme conditions—high temperatures, intense pressures, and rapid rotations—making regular inspections and servicing essential for reliability and efficiency.
Maintenance begins with routine checks performed after every flight cycle. Technicians inspect oil levels, monitor wear on critical components, and analyze sensor data for early signs of fatigue. More in-depth procedures, such as borescope inspections, allow engineers to examine internal components without dismantling the engine, identifying early-stage cracks, erosion, or foreign object damage.
Over time, engines undergo scheduled overhauls, where they are removed from aircraft and disassembled for a deep inspection. Key components like turbine blades, combustors, and bearings may be repaired or replaced to restore performance. Modern predictive maintenance techniques, using AI-driven diagnostics and real-time monitoring, help airlines detect potential failures before they happen, reducing downtime and improving efficiency.
Well-maintained engines can operate for decades, powering thousands of flights. However, no engine lasts forever.
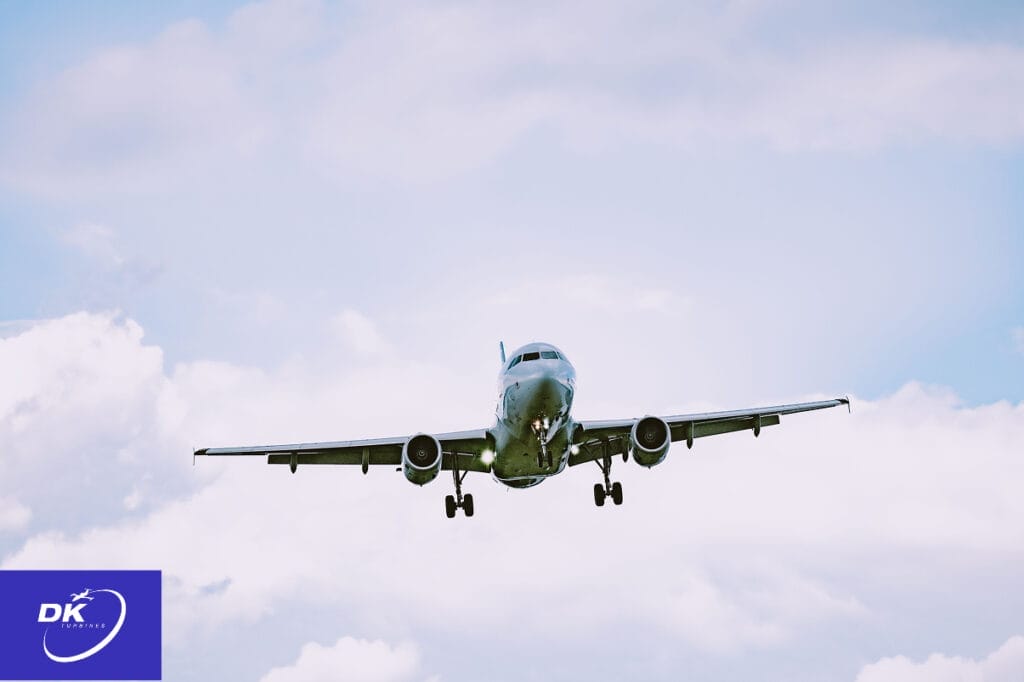
7. Operation: Powering Flight Until Retirement
After years of design, testing, and precision manufacturing, a turbine engine finally reaches the phase it was built for—operation. Installed on an aircraft, it powers thousands of flights, enduring extreme temperatures, high-altitude pressures, and rapid speed variations. Every takeoff, cruise, and landing relies on its ability to perform flawlessly.
Throughout its operational life, the engine follows a strict maintenance schedule to keep it running efficiently. Airlines and operators track engine cycles, monitoring performance metrics to determine when servicing is needed. Predictive analytics and real-time diagnostics help detect early signs of wear, allowing airlines to replace parts before they fail. With proper care, many engines can remain in service for decades.
Eventually, after accumulating thousands of flight hours, an engine reaches the end of its lifecycle. At this stage, it may be retired, overhauled for secondary use in cargo aircraft, or dismantled for parts. High-value materials like titanium and nickel alloys are often recycled, while certain components find new life in refurbished engines.
Even as one engine retires, new advancements continue to shape the next generation of turbine technology. With a growing focus on sustainability, future engines will integrate alternative fuels, hybrid propulsion, and more efficient designs, ensuring the evolution of aviation continues for generations to come.
From Blueprint to Sky: The Life of a Turbine Engine
Turbine engines are the beating heart of modern aviation, powering everything from commercial airliners to high-performance military jets. But these marvels of engineering don’t simply appear on aircraft—they go through a meticulous lifecycle, from initial design to retirement.
Each stage, from concept to operation, is a testament to precision engineering, rigorous testing, and continuous innovation. This journey explores how turbine engines evolve, adapt, and ultimately shape the future of flight.