Every time an aircraft takes flight, the lives of hundreds depend on the reliability of thousands of individual parts working in perfect harmony. Behind this reliability lies a complex, multi-layered testing process that represents one of humanity’s most comprehensive approaches to safety engineering.
From raw materials to integrated systems, each component undergoes rigorous evaluation designed to identify potential failures long before they could occur in service.
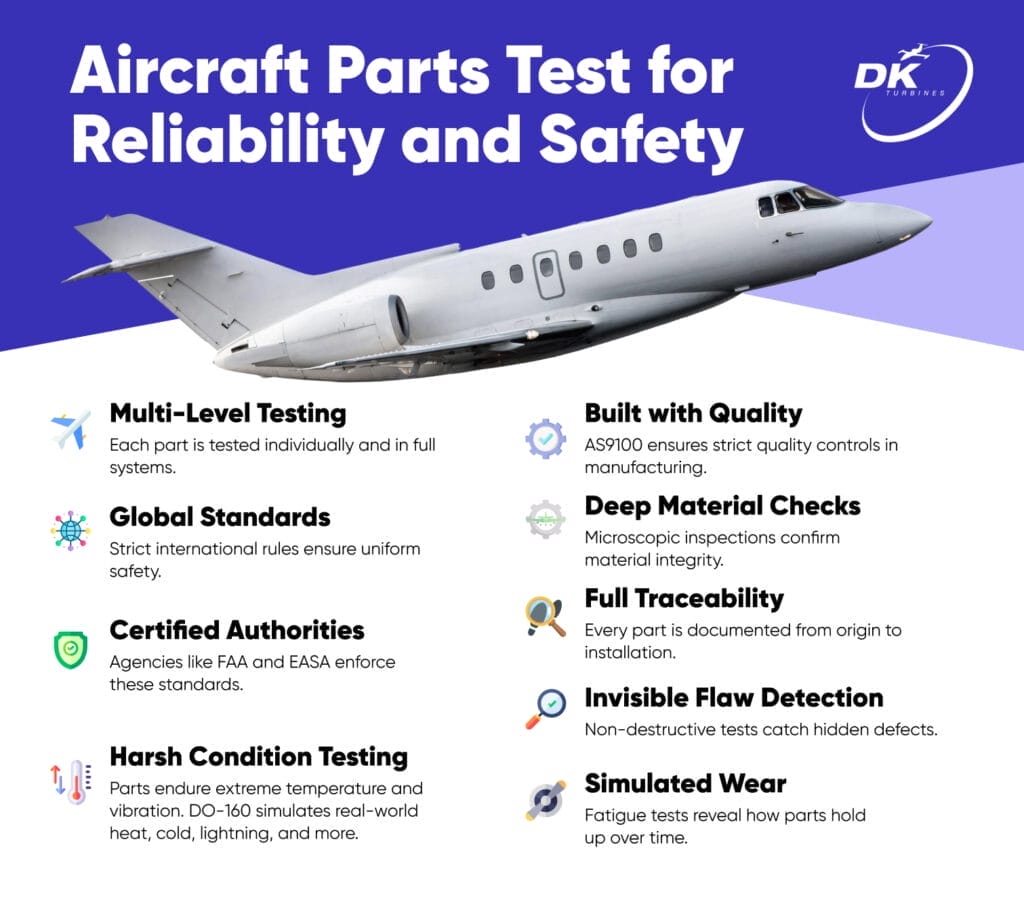
The Regulatory Framework
When it comes to aircraft parts, nothing flies without first passing through one of the most rigorous regulatory frameworks in any industry. This isn’t just bureaucracy at work—it’s a carefully crafted safety net designed to catch any potential issue before it ever leaves the ground.
The Guardians of Aviation Safety
The Federal Aviation Administration (FAA) in the United States and the European Union Aviation Safety Agency (EASA) stand as the primary gatekeepers of aviation safety in their respective regions. But they’re far from alone in this mission. Two particularly critical standards that govern aircraft parts are:
DO-160 is an RTCA standard that might not make headlines, but it’s absolutely critical to ensuring parts can withstand the environmental conditions they’ll face. This standard specifies test procedures for everything from temperature and altitude to lightning strikes and fluid susceptibility. Think of it as the “extreme weather training” that every part must endure before earning its wings.
AS9100 takes the already-stringent ISO 9001 quality management system and adds aviation-specific requirements. It ensures that manufacturers don’t just make parts—they create them within a comprehensive quality ecosystem that addresses the unique risks of aerospace operations.
Other authorities like Transport Canada, Japan Civil Aviation Bureau (JCAB), and Brazil’s National Civil Aviation Agency (ANAC) maintain their own oversight, often working in harmony through bilateral agreements to ensure consistent standards across international boundaries.
Certification Requirements
Before any part can be installed on an aircraft, it needs proper certification. Federal Aviation Regulations (FARs) in the US and Joint Aviation Requirements (JARs) in Europe establish the baseline standards that must be met.
Parts generally fall into one of several certification categories:
- Type Certificate (TC): For complete aircraft designs
- Supplemental Type Certificate (STC): For modifications to existing designs
- Parts Manufacturer Approval (PMA): For replacement parts
- Technical Standard Order Authorization (TSOA): For parts meeting specific performance standards
The path to certification isn’t a simple checkbox exercise—it’s a comprehensive journey that involves rigorous testing, validation, and documentation at every step.
How Regulations Evolve
Aviation regulations aren’t static documents gathering dust on shelves. They’re living frameworks that evolve with each lesson learned—often paid for at a steep price.
Take the case of aircraft wiring standards. After the TWA Flight 800 tragedy in 1996, investigations revealed potential issues with fuel tank wiring. This led to sweeping changes in how wire insulation is tested and certified, resulting in the development of more stringent flammability requirements.
Similarly, the discovery of metal fatigue issues in early jet aircraft led to completely new testing protocols that are now standard across the industry. Each regulatory update carries with it a story—often one that prevented future incidents through the lessons learned.
The Documentation Trail
In aviation, a part without documentation might as well not exist. Traceability isn’t just important—it’s absolutely essential. Every aircraft part must have a documented history from cradle to grave.
Why does this matter so much? Because when you’re flying at 37,000 feet, you need absolute confidence that the critical component keeping you aloft wasn’t manufactured on someone’s garage workbench.
Traceability provides:
- Verification that parts were made to proper specifications
- Confidence that testing was performed correctly
- The ability to track batch issues if problems are discovered
- Protection against counterfeit or unapproved parts entering the supply chain
Each part carries its own “biography”—from raw material certification to manufacturing data to installation records. This unbroken chain of documentation ensures that when maintenance crews install a part, they know exactly what they’re working with.
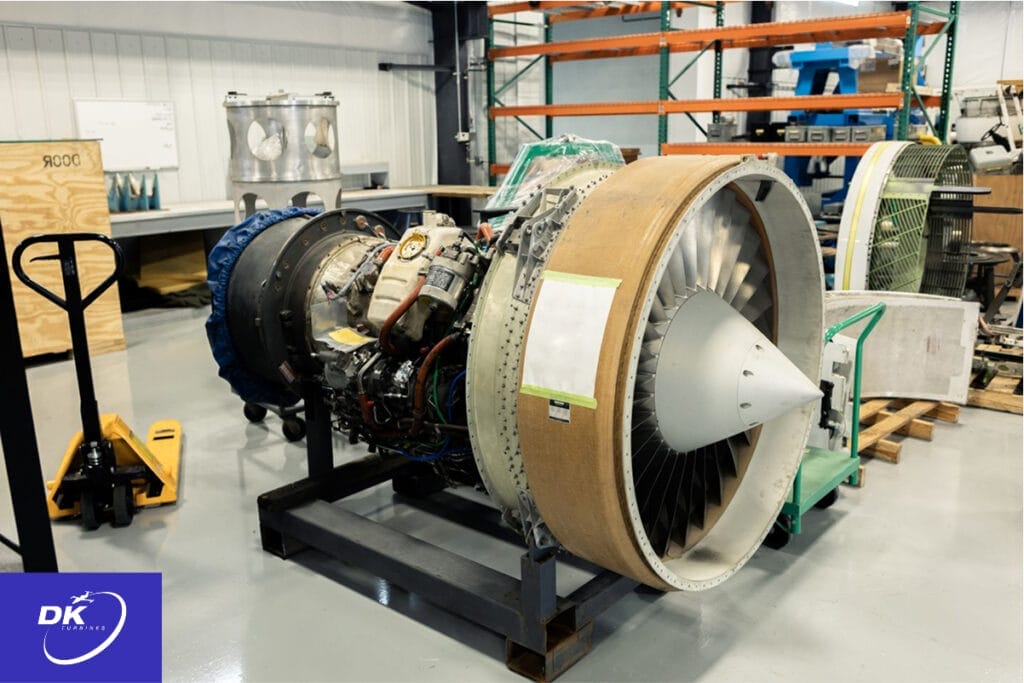
Materials Testing
Every aircraft part depends on precisely selected materials that must perform under extreme conditions. The rigorous testing these materials undergo ensures they can withstand the demands of flight for thousands of hours.
Metallurgical Analysis
The molecular structure of aviation metals directly impacts safety and performance. Metallurgical testing examines chemical compositions and microstructures to verify material properties.
Engineers use spectrometry to confirm exact material makeup and microscopy to reveal grain structures invisible to the naked eye. These tests detect microscopic impurities or structural irregularities that could lead to failures under flight stresses.
Modern aircraft require increasingly sophisticated alloys—combining aluminum with lithium for weight reduction or nickel with chromium for heat resistance. Each composition must be verified to meet exact specifications before manufacturing begins.
Non-Destructive Testing
Non-destructive testing (NDT) methods examine parts without damaging them—crucial for both manufacturing quality control and in-service inspections.
X-ray imaging reveals internal structures, while ultrasonic testing uses sound waves to detect hidden flaws. Dye penetrant testing highlights surface cracks when fluorescent liquids seep into microscopic defects. Eddy current testing can identify subsurface issues in electrically conductive components.
These techniques have evolved from basic inspection tools to sophisticated systems that can create detailed 3D representations of part interiors, detecting flaws as small as 0.001 inches in critical components.
Fatigue Testing and Stress Analysis
Aircraft parts rarely fail suddenly—they typically succumb to fatigue after thousands of stress cycles. Fatigue testing subjects materials to repeated loading patterns that simulate decades of service in compressed timeframes.
Stress analysis techniques like finite element analysis create detailed models showing exactly where forces concentrate, helping engineers eliminate weak points. Test rigs apply cyclical stress patterns while monitoring for early failure indicators.
This approach has dramatically improved modern aircraft reliability. Components now routinely endure testing equivalent to multiple service lifetimes before certification.
Environmental Testing
Materials must perform across extreme environmental conditions. Temperature testing ensures functionality from subzero high-altitude conditions to the intense heat near engines. Humidity chambers assess moisture effects, while salt spray tests accelerate corrosion to identify vulnerabilities.
Environmental testing also subjects parts to vibration, pressure changes, and fluid exposure—often simultaneously—to simulate real-world operating conditions.
These combined environmental tests replicate the harshest conditions parts will face, ensuring they maintain their properties throughout their service life. This testing provides the confidence that when conditions get tough at 37,000 feet, every component will continue performing exactly as designed.
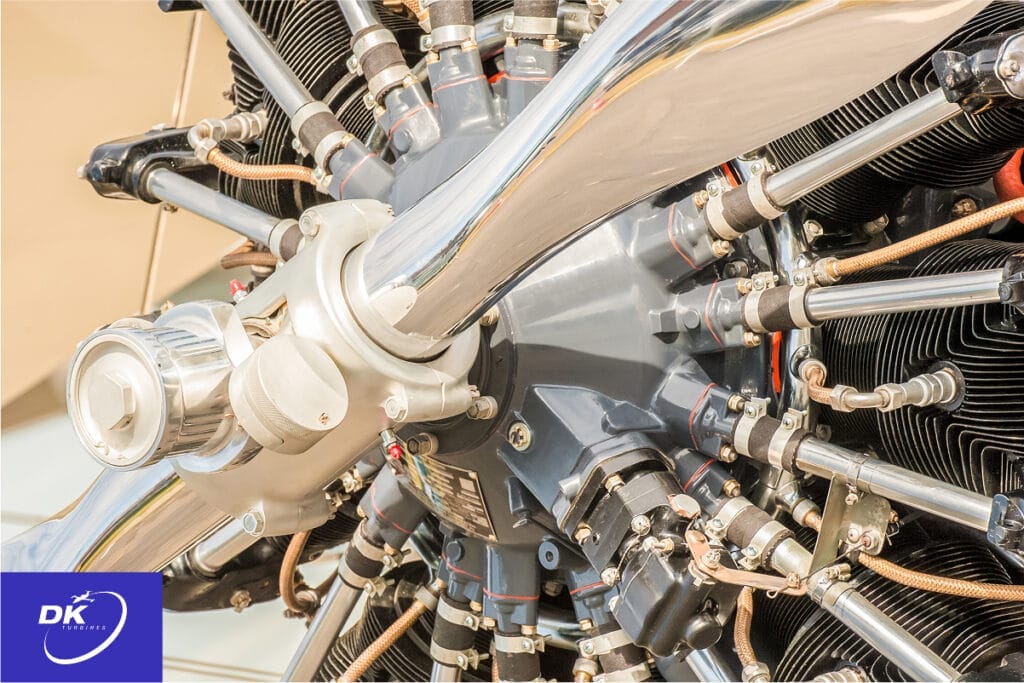
Functional Testing
Even the highest quality materials can’t guarantee performance without rigorous functional testing. This critical phase ensures each component works as designed—both individually and as part of complex systems.
Component-level Testing
Before integration, each individual part undergoes specific testing tailored to its function. Actuators are cycled thousands of times to verify consistent performance. Valves are pressure-tested beyond normal operating limits. Electronic components undergo power cycling at temperature extremes.
These targeted tests verify that each component meets its specific performance requirements. A fuel pump, for example, must deliver precise volumes at specified pressures while maintaining electrical efficiency—each parameter measured and verified independently.
Systems Integration Testing
Aircraft parts rarely operate in isolation. Systems integration testing examines how components interact within larger systems. A seemingly perfect valve might perform differently when receiving electronic signals from an actual aircraft control system.
Integration testing creates test benches that simulate real aircraft systems, often connecting actual components to specialized test equipment that replicates aircraft inputs and loads. This reveals compatibility issues, signal timing problems, or unexpected interactions between components that individual testing can’t catch.
Performance Under Normal Conditions
Once components pass initial functional tests, they face evaluation under standard operating conditions. These tests verify performance within the expected operating envelope—normal temperatures, pressures, electrical loads, and mechanical stresses.
Engineers measure factors like response times, accuracy, power consumption, and heat generation during continuous operation. Tests might run for hundreds of hours, ensuring consistent performance throughout typical flight profiles from takeoff to landing.
Performance Under Extreme Conditions
Perhaps most critical is how components perform when conditions aren’t ideal. Testing under extreme conditions intentionally pushes parts beyond normal operating parameters.
Low-voltage testing ensures electrical components function during power fluctuations. Cold-start testing verifies operation at minimum temperatures. Maximum load testing confirms performance margins under stress. These extreme condition tests reveal the true performance envelope and safety margins of aircraft components.
Durability and Reliability Testing
Aircraft parts don’t just need to work correctly—they need to work consistently for thousands of hours between maintenance intervals. Durability and reliability testing ensures components deliver years of dependable service.
Accelerated Life Testing
Time is a luxury engineers don’t always have during development and certification. Accelerated life testing compresses years of wear into weeks or months by intensifying the factors that cause degradation.
Higher temperatures accelerate chemical reactions and material aging. Increased cycle frequencies compress operational wear. More extreme environmental conditions accelerate corrosion and material breakdown. These accelerated tests follow carefully calibrated models to ensure they produce relevant results that correlate with real-world performance.
MTBF Analysis
Mean Time Between Failures (MTBF) provides a statistical measure of reliability that airlines and manufacturers rely on for maintenance planning and safety assessments. MTBF testing involves operating multiple samples of a component until failure, analyzing the results to predict real-world reliability.
This data drives critical decisions about inspection intervals, replacement schedules, and redundancy requirements. An actuator with an MTBF of 30,000 hours might be scheduled for replacement at 20,000 hours, providing a substantial safety margin before statistically expected failures.
Vibration and Shock Testing
Few environments are as consistently turbulent as an aircraft in flight. Vibration testing subjects components to the continuous oscillations they’ll experience in service—sometimes for hundreds of hours at specific frequencies known to cause resonance issues.
Shock testing simulates sudden impacts, hard landings, or turbulence. Components are literally dropped, shaken, and jolted on specialized equipment that can precisely reproduce specific acceleration profiles. These tests reveal weaknesses in mounting systems, internal structures, and connection points.
Endurance Testing Examples
The aviation industry sets extraordinary endurance standards. Consider the testing of a typical passenger door mechanism: It might undergo 30,000 complete operation cycles—equivalent to decades of service—before certification.
Engine components face even more demanding requirements. Fan blades undergo “blade-out” testing, where engines deliberately operate after catastrophic blade failures to prove containment capabilities. Landing gear systems complete thousands of simulated landing cycles with various loads and runway conditions.
These endurance tests represent the culmination of the testing process—proving that components will continue functioning correctly throughout their entire service life.
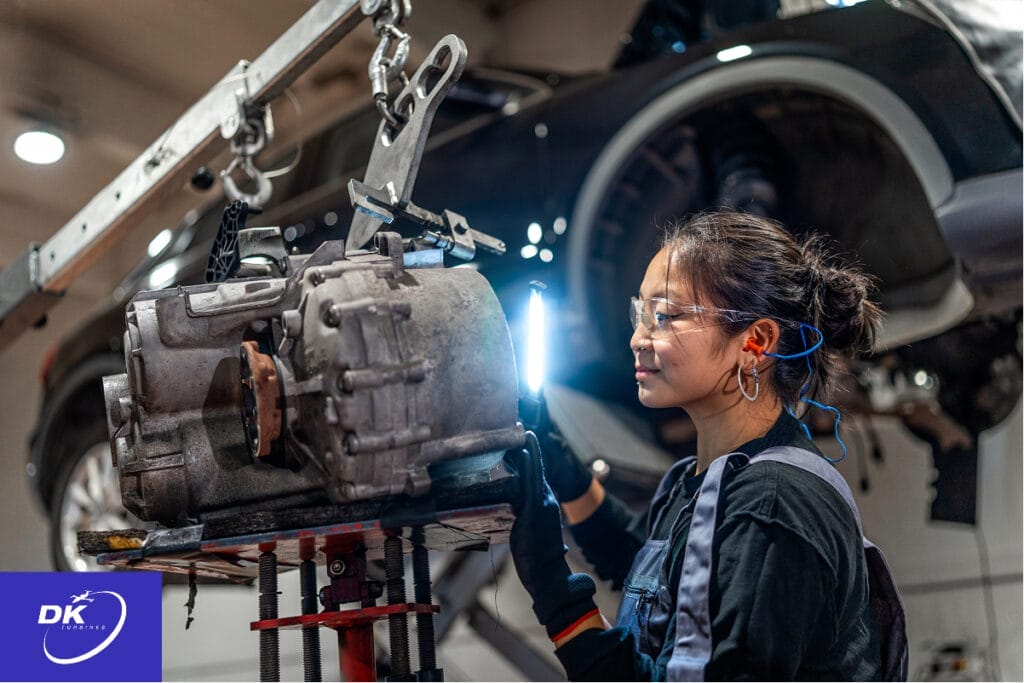
The Human Element in Testing
Despite sophisticated automation, experienced professionals remain the backbone of aircraft parts testing. Their expertise, judgment, and commitment to safety culture make the difference between adequate testing and exceptional quality assurance.
The Role of Experienced Technicians and Engineers
Behind every test stands a team of skilled professionals whose expertise goes beyond running equipment. Experienced technicians notice subtle anomalies—unusual sounds, unexpected measurements, or visual cues that automated systems might miss.
Engineers bring critical analytical skills, interpreting complex data patterns and identifying potential concerns that might not trigger automated alerts. Their experience often leads to testing modifications that address real-world conditions more effectively than standard procedures alone.
This human expertise becomes particularly crucial when investigating unexpected test results. While a machine can identify a deviation from specifications, it takes human insight to determine whether it represents a genuine concern or simply a benign variation.
Quality Control Procedures and Oversight
Quality control in aviation testing involves multiple layers of oversight, documentation, and verification. Independent inspectors verify test procedures, witness critical tests, and confirm results against requirements.
Documentation follows strict protocols, creating audit trails that might be reviewed decades later during aircraft service. Testing equipment itself undergoes regular calibration and certification to ensure accuracy.
Many critical tests require dual verification—two qualified individuals independently confirming results. This redundancy reduces the possibility of oversight errors and ensures compliance with both regulations and internal standards.
The Importance of Safety Culture
Perhaps the most influential human factor is the industry’s deeply ingrained safety culture. Testing professionals understand the consequences of overlooked issues or procedural shortcuts.
This culture encourages questioning assumptions, raising concerns, and prioritizing thoroughness over expediency. Many companies implement non-punitive reporting systems, allowing staff to highlight potential issues without fear of blame.
The result is an environment where “good enough” never suffices. When a test produces borderline results or unexpected behaviors, the default response is further investigation rather than simple acceptance.
How Customer Feedback Drives Improvements
Airlines and maintenance facilities provide crucial real-world feedback that shapes testing evolution. When operators encounter unexpected issues, manufacturers often develop new tests to prevent similar occurrences.
This feedback loop has led to significant testing innovations. For example, wiring harness tests evolved substantially after operators reported chafing issues in specific installation configurations. New test procedures now specifically address these conditions.
Customer input also helps prioritize testing focus. When operators report components that consistently perform beyond expectations, manufacturers analyze these success stories to understand what characteristics contribute to exceptional reliability.
Trust Takes Flight Through Rigorous Testing
Behind every safe flight lies thousands of hours of meticulous testing that most passengers will never see or appreciate. From the regulatory frameworks that establish standards to the advanced computer simulations predicting future performance, the aviation industry has built an extraordinary safety ecosystem that continues to evolve.
This commitment to exhaustive testing explains why air travel remains one of the safest forms of transportation despite the complex systems and extreme conditions involved—a testament to human ingenuity and an unwavering dedication to protecting lives.