Aircraft ground time due to parts unavailability triggers immediate financial consequences that extend far beyond visible operational expenses. While aviation executives typically focus on emergency procurement, expedited shipping, and overtime labor costs, these apparent expenses represent merely a fraction of the total financial impact.
The aviation industry’s competitive environment provides no buffer for the hidden costs that inadequate aircraft spare parts inventory management generates. These expenses do not appear in AOG reports or emergency procurement authorizations. Rather, they systematically erode profitability through revenue losses, operational inefficiencies, and supply chain disruptions that amplify over time.
Comprehending these hidden costs extends beyond improved financial reporting—it requires recognizing that effective spare parts inventory management fundamentally determines the difference between sustainable profitability and operational losses.
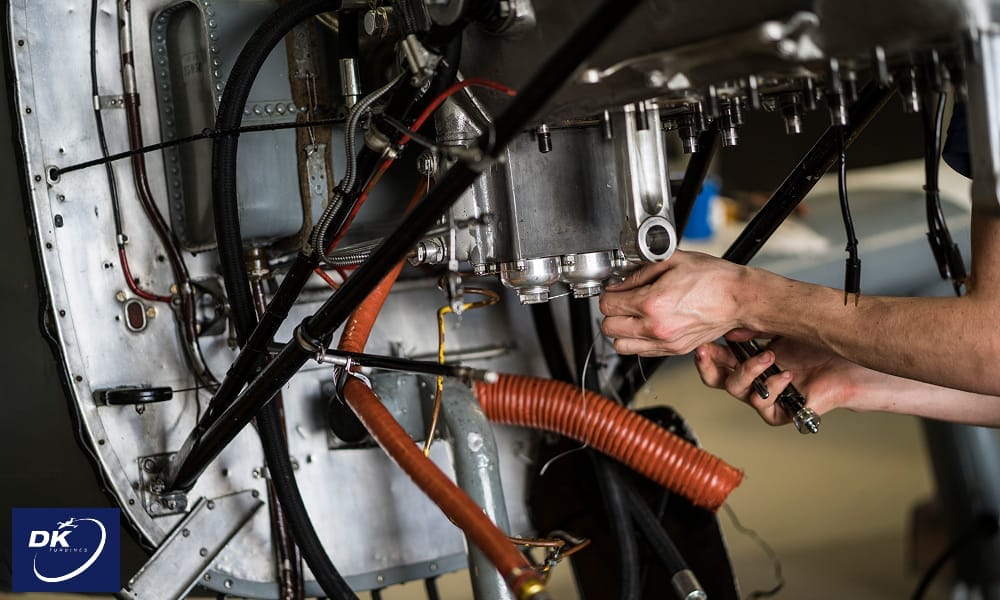
The Emergency Costs Everyone Recognizes
When aircraft maintenance teams encounter critical component unavailability despite inventory management systems indicating sufficient stock levels, immediate financial consequences become evident. The spare parts procurement process can falter, escalating standard component replacements into emergency procurement situations when inventory control systems fail to account for shelf-life expiration or unreported usage.
Expedited shipping expenses escalate rapidly under these circumstances. Transporting critical aviation parts across continents with minimal lead time can cost multiples of the component’s actual value. These expenses become particularly problematic when the required part was available at a closer location, but inventory discrepancies prevented proper location identification.
Over time, labor expenses increase when maintenance operations shift from planned to reactive approaches. Aircraft parts shortages convert routine line maintenance into emergency situations, elevating labor costs while disrupting established maintenance schedules.
Nevertheless, these visible costs remain secondary to the hidden financial damage that occurs when spare parts inventory management fails systematically.
The Hidden Revenue Killers
Aircraft downtime constitutes the most significant hidden cost of inadequate inventory management. Each hour aircraft remain grounded awaiting parts eliminates revenue that cannot be recovered. This represents permanent lost opportunity rather than delayed income, directly impacting operational profitability.
Passenger compensation encompasses more than immediate rebooking expenses. When travelers experience substantial delays due to aircraft maintenance issues, their future booking preferences change. Passengers who encounter maintenance-related delays frequently select competitors for subsequent travel, generating long-term revenue losses that extend beyond the initial incident.
Crew scheduling disruptions generate cascading costs that operators frequently underestimate. When aircraft availability becomes unpredictable due to parts shortages, pilots and flight attendants require hotel accommodations, meal allowances, and transportation to subsequent assignments. Crew scheduling departments work extended hours rebuilding rotations while operators pay premium rates for reserve crews to address operational gaps.
Working capital invested in excess inventory represents another substantial hidden cost. Stockout concerns drive many operators toward over-stocking practices, but maintaining slow-moving engine components with infrequent turnover rates ties up capital that could generate returns in other operational areas.
Storage and handling expenses for aviation parts consume considerable resources annually. Climate-controlled storage for sensitive avionics, specialized handling equipment for heavy components, and labor costs for inventory movements accumulate rapidly. Many operators only recognize the full extent of these costs during comprehensive inventory audits.
Obsolescence generates perhaps the most devastating hidden expense. Rapid technological advancement means components become obsolete faster than anticipated. When aircraft retire early, fleet compositions change, or manufacturers discontinue support for older systems, carefully maintained spare parts inventory loses value immediately.

The Operational Ripple Effects
Inadequate spare parts inventory management creates disruptions that extend throughout entire operations. When inventory management software cannot reliably predict parts availability, MRO planning becomes reactive rather than proactive. Maintenance events that should follow predictable schedules become crisis management situations.
Vendor relationships deteriorate when operators consistently place emergency orders. Suppliers begin categorizing you as high-risk, which impacts pricing negotiations and priority during supply shortages. Poor inventory control can compromise preferred customer status and favorable payment terms that required years to establish.
Fleet availability optimization becomes impossible when parts availability cannot be accurately predicted. Network planning teams might schedule additional aircraft utilization based on projected maintenance windows, only to discover that parts shortages extend downtime beyond planned parameters.
Regulatory compliance becomes exponentially more complex with inadequate aircraft parts inventory management. Every component requires complete traceability documentation, and when systems cannot quickly produce this information, teams spend excessive time manually reconstructing paper trails that should be instantly available.
Supply chain disruptions compound these issues. When forecasting fails to account for supplier lead times and delivery uncertainties, organizations are forced into reactive procurement that elevates costs across the entire parts inventory management system.
Building Effective Inventory Management Systems
Successful aircraft maintenance operations depend on fundamental principles for effective spare parts inventory management. Demand forecasting must extend beyond simple historical averages. Advanced inventory management systems utilize predictive analytics that consider flight schedules, seasonal patterns, fleet utilization rates, and external factors to predict parts demand more accurately.
Real-time visibility across the entire aviation parts network is essential. Whether operating from a single hub or with inventory distributed across multiple stations, instant access to accurate inventory levels, part conditions, and location data is required. This visibility eliminates guesswork that drives both stockouts and over-stocking.
Integration with existing systems is crucial. Inventory management solutions should seamlessly connect with MRO planning software, procurement systems, and financial reporting tools. When these systems function together, manual data entry and reconciliation that create errors and inefficiencies are eliminated.
Establishing metrics that measure operational impact, rather than just inventory turns and stock levels, helps determine the true value of inventory management investments. Monitor AOG events, parts availability rates, and total cost of inventory ownership to gauge system effectiveness.
Inventory managers require tools that provide actionable insights rather than just data. When procurement teams can access real-time information about parts availability, supplier performance, and demand patterns, they can make decisions that prevent problems rather than react to them.
The Strategic Advantage
The hidden costs of poor spare parts inventory management are among the most overlooked threats to aviation profitability—yet they offer one of the greatest opportunities for operational improvement.
When inventory managers have real-time visibility, reliable data, and integrated systems, reactive decisions are replaced with proactive planning. The result? Fewer delays, lower costs, stronger vendor relationships, and higher aircraft availability.
Modern inventory management isn’t just about having the right parts—it’s about building a scalable, efficient operation that supports consistent performance and long-term growth.
Don’t let inefficiencies drain your bottom line. Invest in smarter inventory strategies and start turning maintenance into a competitive advantage.