Success in corporate aviation is measured not just in flight hours but in consistent, reliable operations that keep business moving forward. A crucial part of achieving this reliability lies in identifying the 10 must-have spare parts for corporate aircraft operators should always have to minimize down time and ensure smooth operations. Strategic spare parts inventory, often an overlooked aspect of aviation management, can make or break your operational efficiency.
Whether you operate a single aircraft or manage an entire fleet, knowing which critical components to stock could save you hundreds of thousands in potential downtime costs and help maintain your competitive edge.
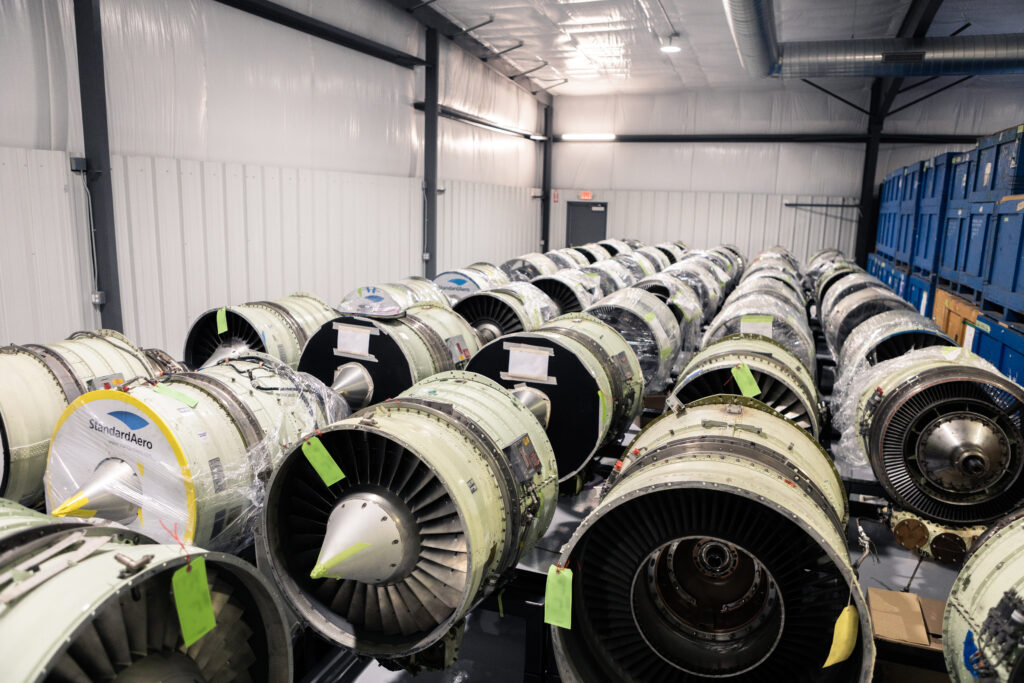
Why Proactive Parts Management Matters
Effective parts management is more than just maintaining inventory—it’s a strategic approach that safeguards your corporate aircraft operations and protects your bottom line.
Aircraft on ground (AOG) situations represent one of the most significant financial risks in corporate aviation. With daily costs potentially reaching $150,000, a grounded aircraft impacts more than just immediate operations—it disrupts schedules, strains client relationships, and creates cascading logistical challenges. A well-managed parts inventory can prevent these costly situations, turning what could be a multi-day disruption into routine maintenance.
Regulatory compliance adds another critical dimension to parts management. The Federal Aviation Administration (FAA) mandates strict requirements for part documentation, maintenance histories, and certification standards. Having the right parts on hand isn’t just about convenience—it’s about maintaining continuous compliance with Airworthiness Directives and Service Bulletins while avoiding potential fines and operational restrictions.
Balancing inventory costs against operational reliability requires careful consideration. While maintaining a comprehensive spare parts inventory typically requires 15-20% of an aircraft’s annual operating budget, this investment must be weighed against the far steeper costs of unexpected downtime and emergency parts procurement. The goal is to maintain optimal operational readiness while keeping inventory-carrying costs manageable through strategic planning and supplier partnerships.
Essential Spare Parts List
1. Engine Components
At the heart of your aircraft’s performance are its engine components. Essential spares should include fuel nozzles and filters, which require regular replacement to maintain optimal fuel flow and prevent contamination.
Keep ignition components like spark plugs and igniters on hand, as these typically need replacement every 300-400 flight hours. Pay special attention to common failure points such as fuel control units and temperature sensors, which can ground an aircraft if not readily available.
2. Landing Gear Components
Your landing gear system faces stress during each takeoff and landing. Stock brake pads and rotors, as they typically require replacement every 150-200 landings. Maintain spare tire assemblies to address wear and potential damage during operations. Hydraulic seals and O-rings are critical yet inexpensive components that can prevent costly repairs if replaced proactively.
3. Avionics Spare Components
Modern corporate aircraft rely heavily on sophisticated avionics. Keep navigation system backup modules ready for quick replacement to maintain flight capabilities.
Communication system parts like radio components and transponder elements are essential for regulatory compliance. Critical display units should be available as backup, particularly for primary flight displays and engine monitoring systems.
4. Environmental Control System Parts
Passenger comfort and safety depend on reliable environmental controls. Stock essential air conditioning components, including compressors and control valves. Pressurization system parts such as outflow valves and controllers are critical for high-altitude operations. Temperature control sensors should be readily available as they’re prone to occasional failure but vital for system operation.
5. Hydraulic System Components
A reliable hydraulic system is crucial for safe operation. Maintain spare pumps and actuators for critical flight control systems. Hydraulic filters require regular replacement to prevent system contamination. Keep pressure-sensing devices on hand, as they’re essential for system monitoring and troubleshooting.
6. Electrical System Spares
Your aircraft’s electrical system demands consistent attention. Stock various circuit breakers as they protect vital systems from electrical faults. Generator components, including voltage regulators and brushes, require periodic replacement. Essential lighting elements, particularly those required by regulations, should always be available.
7. Cabin Interior Components
While often overlooked, cabin components are crucial for operational readiness. Maintain emergency equipment spares to ensure compliance with safety regulations. Keep seating components like seat belt mechanisms and recline actuators available. Cabin pressurization parts, including air vents and pressure relief valves, are essential for passenger comfort and safety.
8. Fuel System Parts
Reliable fuel systems are non-negotiable. Stock replacement fuel pumps for both main and auxiliary systems. Keep filters and strainers on hand for regular maintenance intervals. Fuel quantity sensors are critical for accurate fuel management and should be readily available.
9. Safety Equipment
Safety equipment requires constant readiness. Maintain emergency exit components, including handles and lighting systems. Stock fire suppression system parts, including sensors and discharge nozzles. Keep first aid kit replacements current to meet regulatory requirements.
10. Documentation and Tools
Proper maintenance requires the right tools and documentation. Maintain calibrated testing equipment for system checks. Stock specialized maintenance tools specific to your aircraft model. Keep technical documentation updated and readily accessible for maintenance personnel.
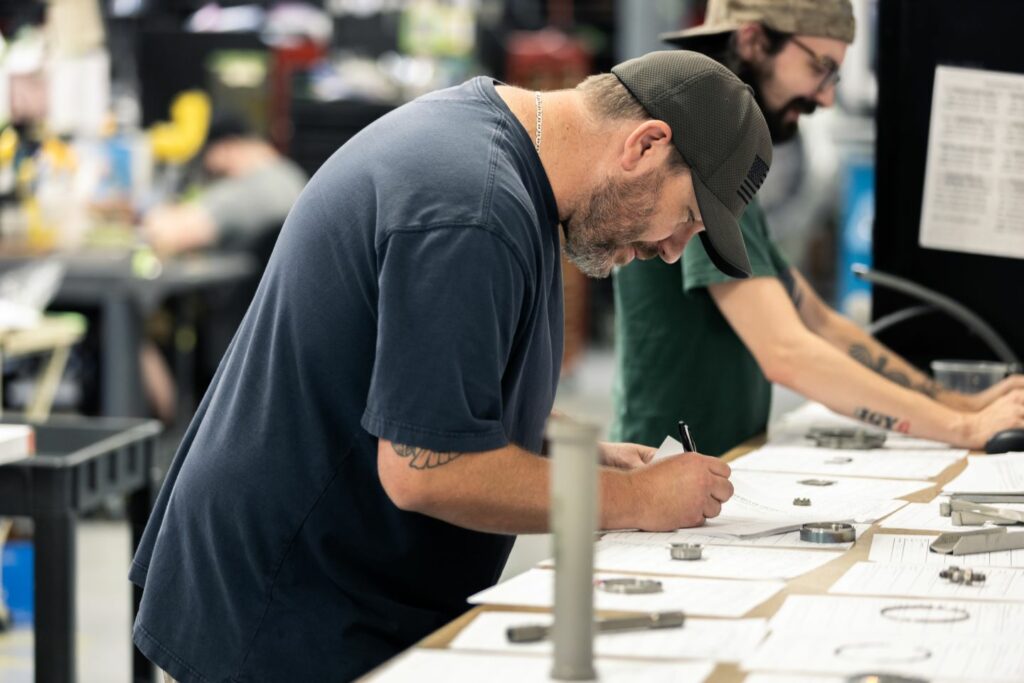
Best Practices for Inventory Management
Proper storage and tracking of aircraft spare parts is just as crucial as having the right parts on hand. Implementation of industry best practices makes sure your inventory remains airworthy, traceable, and ready when needed.
Storage Requirements and Conditions
Aviation parts demand precise environmental controls to maintain their integrity. Maintain a clean, climate-controlled storage area with temperatures between 65-75°F and humidity levels below 60%. Use specialized packaging and protective materials for sensitive components like avionics and electronic parts.
Implement a clear organizational system with dedicated areas for different component categories and ensure all parts are properly labeled with part numbers, serial numbers, and shelf-life dates. Keep ESD (Electrostatic Discharge) protection protocols in place for sensitive electronic components.
Inventory Tracking Systems
Modern inventory management requires sophisticated tracking solutions. Implement a digital inventory management system that can track part numbers, quantities, locations, shelf life, and certification documentation.
Consider using barcode or RFID technology for real-time inventory updates and automated reordering triggers. Your system should generate alerts for minimum stock levels, approaching expiration dates, and required certification renewals. Regular inventory audits help maintain accuracy and identify trends in parts usage, enabling more precise forecasting.
Supplier Relationship Management
Building strong relationships with reliable suppliers like DK Turbines is essential for efficient parts management. Establish relationships with multiple approved vendors to ensure supply chain resilience but maintain preferred supplier agreements for critical components. Develop clear communication channels for expedited orders during AOG situations.
Regular performance reviews with suppliers help maintain service quality and can lead to better pricing and priority access to hard-to-find parts. Consider vendor-managed inventory programs for frequently used components to optimize stock levels and reduce carrying costs.
Elevate Your Aircraft Operations: The Strategic Spare Parts Advantage
Maintaining a well-managed spare parts inventory is the cornerstone of efficient corporate aircraft operations.
By carefully balancing inventory investments against operational demands, implementing robust storage and tracking systems, and building strong supplier relationships, operators can significantly reduce AOG risks and maintain peak operational readiness. Remember that each component in your inventory represents not just a part but a commitment to safety, reliability, and operational excellence.
Contact DK Turbines today to ensure your aircraft’s critical spare parts needs are met with precision and expertise.